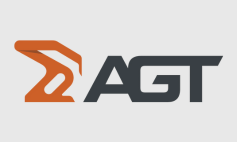
AGT Robotics
AGT Robotics provides flexible robotic systems for the metal fabrication industry. Our solutions will considerably improve the productivity and the quality of manufacturers’ products.
Beammaster
THE BEAMMASTER IS THE #1 SELLING ROBOTIC WELDING FOR STRUCTURAL STEEL IN THE WORLD.
THE COMMON-SENSE, ALL-INCLUSIVE ROBOTIC WELDING SOLUTION FOR STRUCTURAL STEEL
Simply send a pre-fit beam to the BEAMMASTER and watch it robotically complete the required welds in a fraction of the time it would take a manual welder. When equipped with the optional beam rotators, the entire sequence is completely autonomous as the robot automatically positions the welds into the horizontal position every time.
Robotic welding has historically required a large volume of identical parts in order to be profitable. The BEAMMASTER’s award-winning CORTEX SOFTWARE makes robotic welding possible and profitable with lot quantities of one.
WHY AUTOMATE YOUR FACTORY
Automated
Efficient
flexible
By batch processing an entire 3D building (using TEKLA, SDS2, ADVANCED STEEL, BOCAD and more) CORTEX creates hundreds of unique, tailor-made robotic programs that are ready-to-use on the shop floor – eliminating the need to program each beam individually.
The skilled labor shortage is with us and getting more critical every day. The BeamMaster and LayoutMaster help you to reduce your reliance on skilled labor.
The BeamMaster will produce quality welded assemblies at 3-4 x the speed of your manual operations – without the need for a skilled welder to operate it.
When investing in a robotic system one of the key features to look for is versatility. Some jobs might require greater flexibility from the robot than the fully- automated, CORTEX-powered, beam and column welding.
VERSATILE = WELD MORE STUFF !



THE BEAMMASTER CAN ALSO BE USED TO WELD MISCELLANEOUS ASSEMBLIES.
When investing in a robotic system one of the key features to look for is versatility. Some jobs might require greater flexibility from the robot than the fully-
automated, CORTEX-powered, beam and column welding. The BEAMMASTER can be used like a standard robotic welding system to weld panels, short sub-assemblies, small skids or other miscellaneous assemblies – anything that fits in it’s work envelope.
Mill Shapes
• H-Beam
• HSS
• Channels
Fabricated beams
• Straight
• Tapered
• Double-Tapered
Other Assemblies
• Panels
• Delta Beams
• Other
ELIMINATE UNNECESSARY HANDLING
BEAM ROTATORS & DUAL-ZONE CONCEPT STREAMLINES OPERATIONS
Spend your time adding value, not moving steel around! Once you load your beam inside AGT’s beam rotators, you won’t need the crane again until it’s completely fit and welded, ready for paint. The beam rotation is handled automatically throughout the entire fitting and welding process. The robot and the operator switch zones to optimize efficiency

Auto-Programming
1. Export Model

2. Automatically Generate Programs

NO PROGRAMMING = NO HUMAN INTERVENTION
THE ONLY TRUE NO-PROGRAMMING SOLUTION FOR ROBOTIC WELDING!
This is WHY the BEAMMASTER has quickly become the number one selling robotic welding system for structural steel.
In a typical building there are many similar beams but only a few are ever exactly the same making it impractical to automate using conventional robotic programming methods (teach pendant, offline programming, etc.).
AGT’S CORTEX SOFTWARE was specifically developed for the structural steel industry to automatically batch process an entire building to create completely tailor-made robot programs for each unique beam. It will:
AUTOMATICALLY :
√ Position the beams in the rotators;
√ Read the weld information from CAD or auto-generate welds as per your specifications
√ Generate welding paths
√ Associate welds with the correct weld schedule
√ Generate the joint laser finding paths
√ Generate weld to weld movements
√ Generate the torch maintenance routines
√ Sequence welds to prevent heat distortion
√ Rotate beams to access all faces
√ Convert lengthy, longitudinal welds into stitches and more !
NO PROGRAMMING = NO Programmer
Don’t be fooled by other manufacturers’ claims that their solutions require no-programming. If the software user needs to indicate to the robot what welds to perform by clicking on the joint and specifying the weld leg size, or position the beam inside the robotic system…
THAT IS PROGRAMMING! It may be a simpler more graphical method than generating lines of code but it still requires a skilled user (programmer) and adds time and cost to your process! ONLY CORTEX is a true no-programming solution.
With CORTEX, only a few mouse clicks are necessary to start the program creation process for an ENTIRE BUILDING. The result is hundreds of unique robot programs created totally automatically.
dimensions

Fence to fence – 97′
EWZ 1 – 34′
EWZ 2 – 34′
EWZ 1 + 2 – 80′
Height – 12′
Fence-to-fence – 29.57 m
EWZ 1 – 10.36 m
EWZ 2 – 10.36 m
EWZ 1 + 2 – 24.38 m
Height – 3.7 m
Welding Specification
Typical welding speed – fillet welds (2f) | 20.0 in/min for 3/16’’ weld 15.5 in/min for 1/4’’ weld 10.0 in/min for 5/16” weld |
8.4mm/s for 4.8 fillet weld 6.5mm/s for 6.4mm fillet weld 4.6mm/s for 8mm fillet weld |
Gap detection | No gap detection | |
Joint detection | Lase Touch Sensing | |
Process and position |
MCAW – Spray and pulse transfer – Horizontal (2F) or |
|
Wire | MCAW: Hobart Fabcor Edge 0.045″ Diameter (1.2mm) or GMAW: Lincoln Electric Super Arc L-59 0.045″ (1.2mm) |
|
Wire classification | MCAW: A5. 18, A5. 18M: E70C-6M H4 / CSA W48-06: E491C-6MJ-H4 GMAW: A5. 18, A5. 18M: ER70S-6 / CSA W48-06: ER49S-6 |
|
Shielding gas | 85%At-15%CO2 Mix | |
Surface finish | All parts and beams must be clean with no excessive mill scale. Database includes procedures for both Sandblasted surfaces and mill scale. Highest quality is obtained on Sandblasted surfaces. Slower welding speeds are used for Mill scale surfaces. |
Parts specifications
W Beam

Imperial
Section | Min | W6 x 14 |
Max | W48 | |
Length | Min | 12′ |
Max | 80′ |
Metric
Section | Min | W150 x 22 |
Max | W1220 | |
Length | Min | 3.62m |
Max | 24.4m |
HSS

Imperial
Section | Min | 6″ x 6″ x 0.188 |
Max | 20″ x 20″ | |
Length | Min | 12″ |
Max | 80′ |
Metric
Section | Min | 152 x 152 x 4.8mm |
Max | 558mm x 558mm | |
Length | Min | 3.62m |
Max | 24.4m |
Connectors

rotators specifications

W Beam
Imperial
Section | Min | W8 |
Max | W48 | |
Length | Min | 12′ |
Max | 50′ |
Metric
Section | Min | W200 |
Max | W1220 | |
Length | Min | 3.62m |
Max | 15.2m |